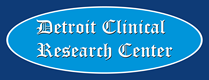

Our Services |
---|
Site Management |
Biostatistics |
IRB |
Lab Services |
Data Management |
Regulatory Services |
Feasibility Studies |
Volunteers |
---|
Trial Information |
Investigators |
FAQ |
Enrollment & Requirements |
Career |
---|
Join our Team |
Contact us |
Contact DCRC |
Six Sigma Processes
We utilize the powerful tools of the six sigma process in supporting our projects. Our SOP’s are based on Six Sigma and Failure modes analysis to make sure we deliver superior quality services.
Overview of the Six Sigma Processes:
Six Sigma is a quality control process based on the statistical measure of standard deviation. This process has expanded to a world class quality control system to provide a better product or service faster and at a lower cost.
Six Sigma Process Introductions:
Sigma is a term use in statistics to represent standard deviation, an indicator of the degree of variation in a set of measurements or process. Six sigma is a statistical concept that measures a process in terms of defects at the six sigma level; there are only 3.4 defects per million opportunities which means, at this level, the process is nearly perfect. It is also a philosophy of managing that focuses on eliminating defects through practices that emphasize understanding, measuring and improving processes.
The Six Sigma methodology can be understood as a formal approach of efficiently and effectively manage business, achieve process improvements and solve problems and its philosophy is focused on process control and improvement by the usage of statistical tools.
In the past, it was common to determine the price of product by adding the cost to the expected profit, but nowadays the price is defined by the market.
Therefore, maximizing profits and gaining a competitive advantage is actually obtained by reducing operational costs. Reducing costs is highly correlated with increasing quality at different levels was it planning, production or distribution. The revolution that Six Sigma brings involves a scientific and repeatable fact-based methodology that enables organizations to measure process improvement on a common scale.
Six Sigma - The Basics:
The Greek letter “σ” represents the standard deviation, or in other words, the process dispersion. Most of the cases the data collected and organized follow a normal distribution.
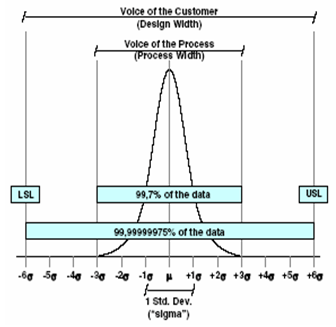
The Voice of the Process is represented by the natural variability of the process, and the Voice of the Customer, by the specified tolerances (Upper and Lower limits). The process capability is the relationship between the mentioned process variation and the Customer’s requirements. A process can be considered Six Sigma, when six Standard deviations between the mean and the Customer’s requirements can be fitted. It leads to a bold 3.4 defects per million. The greater the number of Sigma’s, the most controlled, the process is, fewer chances of defects, and higher expected profit.

Six Sigma - The Process:
The Six Sigma methodology is based on a well defined roadmap divided into five main steps: Define Measure, Analyze, Improve, and Control – DMAIC.
This tool is very efficient because it is a well organized method of asking the right questions, identifying the proper inputs required to answer them, and the outputs. In other words, it can be seen as an oriented brainstorming.
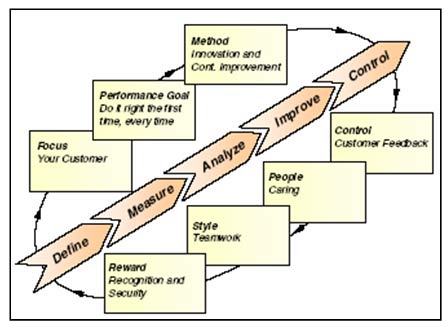
Improvement teams use the DMAIC methodology to root out and eliminate the causes of defects:
D: Define a problem or improvement opportunity.
M: Measure process performance.
A: Analyze the process to determine the root causes of poor performance; determine whether the process can be improved or should be redesigned.
I: Improve the process by attacking root causes.
C: Control the improved process to hold the gains.
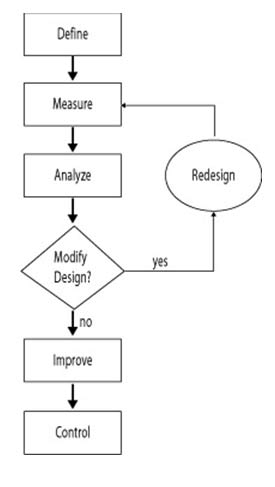
Define:
Seek and prioritize opportunities; makes the business case; real identification of the problem and goal statement; identify and designate .The team for the project; and describe the (as is) process, customer and requirements
Measure:
Decide what and where to measure; develop and agree on operational definitions; identify appropriate data source(s); prepare collection forms and sampling plan; and test, refine and implement measurement
Analyze:
Examine process and data; (This is where the questions of feasibility, redesign or a new design take place and the assumptions of the process are reevaluated and further analyzed as appropriate); develop root cause hypothesis; and investigate as well as verify the root cause.
Improve:
Generate solution ideas; narrow ideas and develop proposed solutions; (select best solution to achieve the goal); plan and test improvement solution; and evaluate, refine and expand proposed solution(s).
Control:
Plan ongoing measurement; develop appropriate and applicable documentation; prepare revision and response plans; and maintain as well as expand the gain.
Design for Six Sigma
Design for Six Sigma is defined as:
- A methodology for designing new products and / or process.
- A methodology for re-designing existing products and / or process.
- A way to implement the six sigma methodology as early in the product or service life cycle as possible.
- A way to exceed customer expectations
- A way to gain market share
- A strategy toward extraordinary return on investment.
In the new era competitive world, new technologies will be developed and improved and will eventually be obsolete for the need of more advanced technologies. In this dynamically changing world, product cycles are expected to last for just a few months. To meet these demanding requirements product developers have to develop products in the shortest amount of time that is safe, reliable, and competitive.
For the majority of organizations, long-term success is tied directly to the new product development process. Tomorrow’s revenue and growth are tightly bound to how successful organizations are at launching new products. Understanding what aspects of a product are key to customer’s perceptions of a product is critical in ensuring a successful product. Value attracts customers. Quality earns respect and innovation differentiates one product from another. Actively building in these items into a product development process, to drive it, provides a key way to ensure product success. This is the key to Design for Six Sigma (DFSS). DFSS provides a proactive, systematic method to build important customer requirements into all related aspects of product development process that can be measured, verified and optimized. DFSS provides a way for customers to incorporate performance characteristics into their product manufacturing and development processes. Manufacturing and development processes can then be optimized to meet those customer requirements using specific and quantifiable metrics. Customers can then manage quality levels against a specific budget. DFSS is therefore able to provide a rigorous methodology to further ensure planned product excellence.
So, briefly Design for Six Sigma is nothing but DMADV (Define, Measure, Analyze, Design and Verify) and DMADOV (Define, Measure, Analyze, Design, Optimize, and Verify) which Focuses on the up-front design of the product and process. The benefits of DFSS are more difficult to quantify and tend to be more long-term. It can take six to 12 months after the launch of the new product before you will obtain proper accounting on the impact.
Unlike the DMAIC methodology for Six Sigma, the phases or steps of DFSS are not universally recognized or defined -- almost every company or training organization will define DFSS differently. Most times a company will implement DFSS to suit their business, industry and culture.
Business Challenges:
- Customers demand product excellence.
- Excellence is defined as the ideal balance of product attributes, such as Cost, Quality, Performance, Aesthetics, Packaging, etc.
- Manage variability of customer-facing product attributes.
- Improve the predictability and capability of the product development process.
- Market demands reduced costs and increased profitability.
- Increase product development process effectiveness.
- Directly meet customer requirements.
- More effectively manage product development costs.
Process Objectives:
- Effectively identify and manage key customer-facing product attributes
- Design products to specific performance metrics against those attributes
- Identify contributing product design elements and processes that affect those attributes
- "Design in" customer-facing product attribute quality levels directly into contributing product development processes
- Manage, verify, balance & optimize customer-facing product attributes throughout the product
Development process
Benefits of DFSS:
Goal: Create new game-changing products and services which
- Please customers with Six Sigma performance on their cost to the company
- Have Six Sigma reliability
- Have Six Sigma manufacturability
- Have high performance/cost ratios
Payoffs:
- Quality designed in from the start
- Revenue growth: customer delight, market share, volume, and price
- Warranty cost reductions
Characteristics of a Successful DFSS Implementation:
- Commitment and leadership from the top
- Measurable, “stretch” goals for each project
- Accountability for project success
- Involvement and support of everyone
- Training and implementing an extremely powerful, yet easy to use toolset for predicting quality and making tradeoffs before the product or process is even built